Inside the vessel of the biggest fusion device, first wall panels will protect the chamber housing the fusion reaction from the neutrons and other energetic particles that are produced by the hot plasma (150 million °C). Given the fact that this is a-first-of-a-kind component, much effort has been put in developing conceptual designs and small-scale prototype. During his PhD at Stockholm University, Yuan Zhong investigated with F4E the feasibility of additive manufacturing of tungsten as irradiation barrier and developed a full-scale prototype of first wall cooling panel using two additive manufacturing technologies (Laser powder bed fusion and Electron beam powder bed fusion). With his team, Yuan Zhong worked on parameter development for additive manufacturing (AM) of 316L powder, material verification and validation and finally the production.
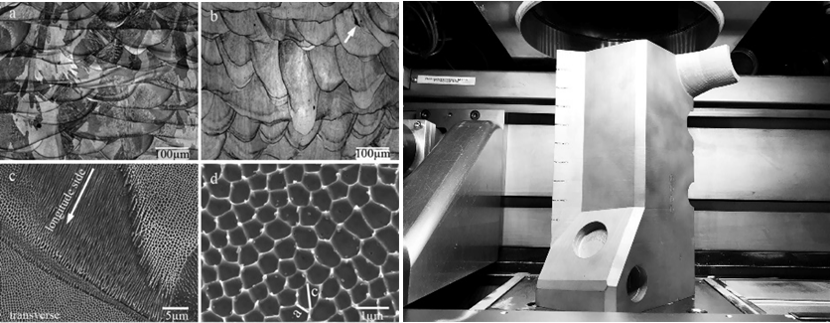
An opportunity to broader the use of additive manufacturing in the automotive industry.
Thanks to the collaborations with F4E, the fusion scientist discovered the super strong and ductile property of AM 316L steel and disclose the mechanism that broke the trade-off between strength and ductility. Results obtained by this participation to 3 Grant Agreements revealed the potential of this technology in the fusion field and was organized by Stefan Wikman F4E (Group Leader of Materials & Manufacturing Technologies & Processes Group).
Yuan Zhong also acquired a strong know-how in plotting the process-microstructure-property relations, identifying the best technology for the right application and finetuning the final material property by changing the processing parameters.
Few years later, Yuan Zhong joined Volvo Group as Additive Manufacturing specialist to broader the application of AM technology in the automotive industry. He leverages today on the knowledge acquired during the fusion projects to reduce the cost of AM parts, decrease the lead time compared to traditional counterparts or improve the supply chain with the concept of manufacturing on demand and manufacturing on site.
Better performance, faster lead time and lower cost of AM parts
Automotive additive manufacturing market was valued at US$ 1,570 million in 2020 and is projected to reach at a market value of US$ 13,597.7 million by 2031. Over the recent years, 3D printing technology has gained significant prominence in the automotive sector, helping create several lightweight components and body parts. The AM metal can replace the existing iron-based material and aluminum alloy which are currently used as the main metal materials in automotive. The stronger but also ductile metal material produced by metal AM enables the possibility to redesign and reduce the weight of the existing spare parts in automotive. The weight reduction can further reduce the production cost of the parts. Meanwhile, the reduced weight can reduce the fuel consumption in the automotive lifetime, which is both economical and environmentally good.
Volvo Group has today a core cross functional team with ~10 people are working daily on AM and attributes an advance engineering funding to this research field every year. The company is involved in the Swedish consortium association of AM projects and are working with other companies in Sweden to secure the full potential of AM is utilized.
Volvo Group has today a core cross functional team with ~10 people are working daily on AM and attributes an advance engineering funding to this research field every year. The company is involved in the Swedish consortium association of AM projects and are working with other companies in Sweden to secure the full potential of AM is utilized.
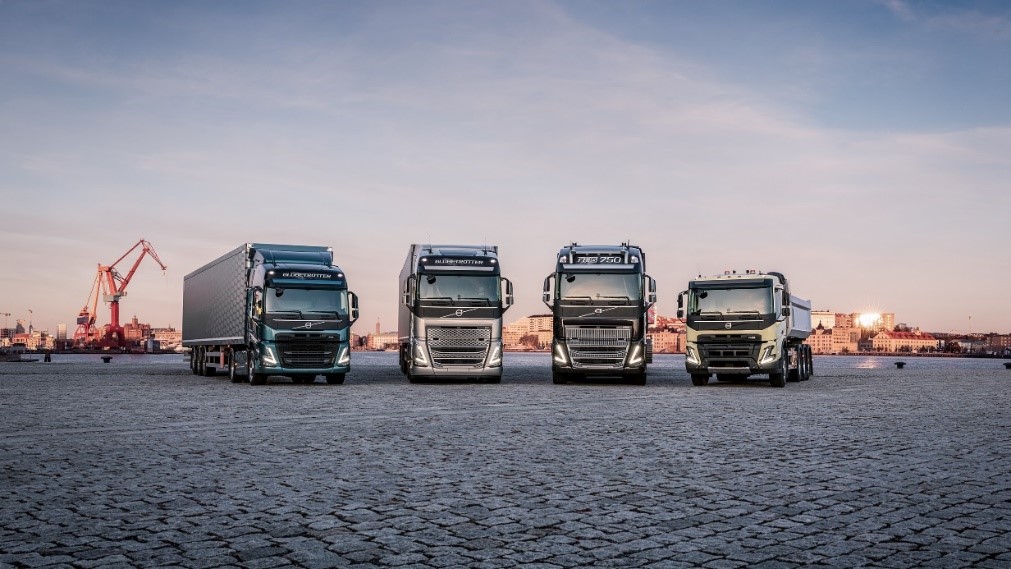